During the end of week 1 and the beginning of week 2, we wrapped up our okapi enrichment boot camp projects. First, we had to complete Pugh screening and scoring matrices to narrow our 36 brainstormed solutions down to 1 solution that we would actually prototype. The Pugh scoring matrix allowed us to evaluate our final nine solutions based on each design criteria and its importance. While these matrices can be painful and tedious to complete properly, they are extremely important to choosing the most promising design solution. The solution that we ultimately chose was a hanging mesh basket that hay or lettuce would stick out of, encouraging the okapi to mimic their natural behavior of pulling leaves off of trees.
On Monday, as an introduction to prototyping, we were tasked with creating a low fidelity prototype of a bajaj, a type of open air taxi used in Ethiopia that is often involved in accidents. The goal of our bajaj was to transport passengers from one place to another safely, but still be open-air. The way that this was tested is by sending each team’s bajaj down a zip-line and crashing it into a table. If the “passengers” (ping pong balls) remained in the bajaj, then our time was recorded, and the fastest time won. Keeping with the traditional open-air bajaj concept, our ping pong balls also had to fall out of the bajaj when it was turned upside down. I worked with Jake, and we created an aesthetically pleasing and safe (if slow) bajaj. Jeremy (the TA) had the fastest bajaj after waxing his zip-line connection with chapstick (which may or may not have been against the rules). His bajaj came down the zip-line in slightly under five seconds.
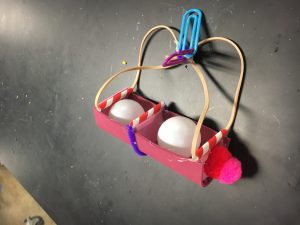
Jake and I’s bajaj. Ours was the self-declared safest bajaj, coming down the zip-line at a solid 25 seconds (compared to the winning bajaj that zip-lined in about 5 seconds).
The next step for the okapi enrichment project was to create a low fidelity prototype of the device for proof of concept. We first made a prototype together as a team, and then each made our own version of the device. Chris’s low fidelity prototype incorporated a cause and effect element that would allow the okapi to receive food when they spun the mesh with their tongue. We decided to modify our original design and prototype to incorporate the spinning element since this would intellectually stimulate the okapi further than a simple hanging basket.
After proving our concept with a low fidelity prototype, we were ready to move on to a medium fidelity prototype. Ours was made from laser-cut wood and netting. A latch on the top of a wooden box opens, allowing the zookeeper to insert grain pellets. The bottom of this compartment has holes, and the top of the attached cylinder has similar holes. As the okapi spin the mesh cylinder with their tongues, the holes will line up and the food will fall so that the okapi can reach and eat it. This prototype completed the desired functions of our device fairly successfully, but used materials that would be unsafe for the okapi. If we were to continue this project in the future, we would build a high fidelity prototype, replacing the netting with chain-link. We would also replace the rectangular box and wood circles with a plastic cylinder and plastic disks.
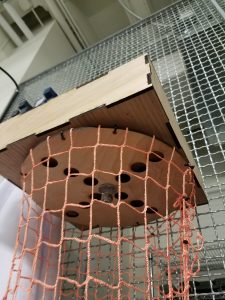
A close up of our low fidelity prototype. These holes allow food in the top compartment to fall into the mesh basket.
On Tuesday afternoon each team gave a presentation about their prototypes, and we were done with boot camp (yay!). On Wednesday morning we heard the pitches for the real projects that we would be working on for the rest of the summer. These included a device for people with diabetes to check their feet for ulcers, a device to help transfer wheelchair users to a higher location, an oxygen calibration device, and a stand to steady people whose feet and legs are being cast for orthotics or prostheses. All of these projects have been worked on in the past and are therefore in various stages of design and prototyping. My first choice project was the wheelchair transfer project, since I have worked extensively with people who use wheelchairs and am interested in working in the field of adaptive and rehabilitative technology.
After we waited in suspense while Dr. Wettergreen, Dr. Hunter, and Jeremy (the TA) deliberated, the project teams were announced. I got my first choice project! I am working on the wheelchair transfer device along with Jake, Bruno, and Christina. Our team name is “Started from the Bottom (Now We’re Here)” (I take full credit for this terrible and amazing team name).
The first thing we did for our new project was to read all of the documentation from the teams that had previously worked on our prototype. We also evaluated the prototype that they had built. It is similar to a salon chair, with the caregiver using a foot pump to lift up the person in the chair. The base is made of polypropylene, and the hydraulic pump clips into this base.The foldable chair, also made of polypropylene and sponge padding, sits on top of the pump. While this prototype works to an extent, it does not meet many of the client’s needs. For instance, it only raises the person five inches, while it should raise them 18 inches. It is also extremely heavy and somewhat expensive (not to mention the fact that it breaks and tips over if you lean too far to the back or side while in the chair). Despite these issues, the prototype does give us a starting point, and is a promising idea. It does not require very much effort from the caregiver to lift the person, and incorporates an adjustable seat back. The team’s design context review and previous failures will also help us create an improved transfer device.
On Thursday, we took part in a needs-finding workshop. This was a workshop in which we tried to gain empathy for the challenges that people with some types of disabilities face. For instance, we were blindfolded and walked around the OEDK. We also had to enter the OEDK while using a wheelchair, and eat cereal with our arms bound. While I recognize that these simulations do not allow us to really feel what it is like to have these disabilities, they allowed us to realize certain things we may not have realized before, like how the elevator is at the very back of the OEDK.
Week 2, like week 1, was both busy and fun. I’m happy to finally get started on our real projects, and I’m so grateful that I am able to work on a project that relates to a field I might want to work in after graduation. Today our team will finish brainstorming both new solution options and modifications to the current prototype. Later, we will meet with our client, a physical therapist at Shriner’s Hospital, to clarify the desired features of the device. I’m excited to see what our team will ultimately decide to build and how the device may be able to assist both wheelchair users and their caregivers, family members, and friends that help transfer them.